The
essence of sintering is that the powder block is heated in an appropriate environment or atmosphere, and through a series of physical and chemical changes, the bonding between powder particles undergoes a qualitative change. The strength and density of the block increase rapidly, and other physical and mechanical properties are also significantly improved. The performance of ceramic materials is not only related to their chemical composition, but also closely related to their microstructure. After the formulation, mixing, forming and other processes are completed, sintering is the key process to obtain the expected microstructure of the material and endow it with various properties.
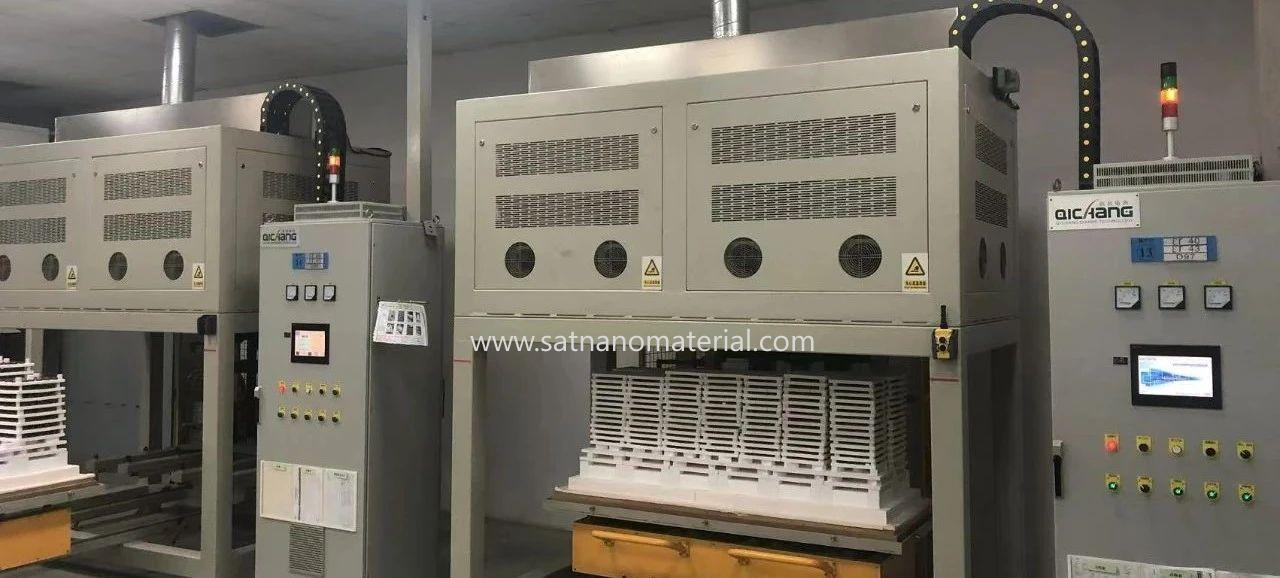
Sintering is a process that reduces pores in the formed body, increases the bonding between particles, and improves mechanical strength. During the sintering process, as the temperature increases and the heat treatment time prolongs, the number of pores decreases and the bonding force between particles increases. When a certain temperature and heat treatment time are reached, the grain size increases and the mechanical strength decreases. According to thermodynamic principles, sintering is a process in which the total energy of a system is reduced. Compared to bulk materials, powders have a large specific surface area, and surface atoms have much higher energy than internal atoms. At the same time, various lattice defects also exist inside the powder particles during the manufacturing process. Any system has a tendency to transition to the lowest energy state, which is the driving force of the sintering process, that is, the transition from the compact to the sintered compact is the process of the system transitioning from a metastable state to a stable state.
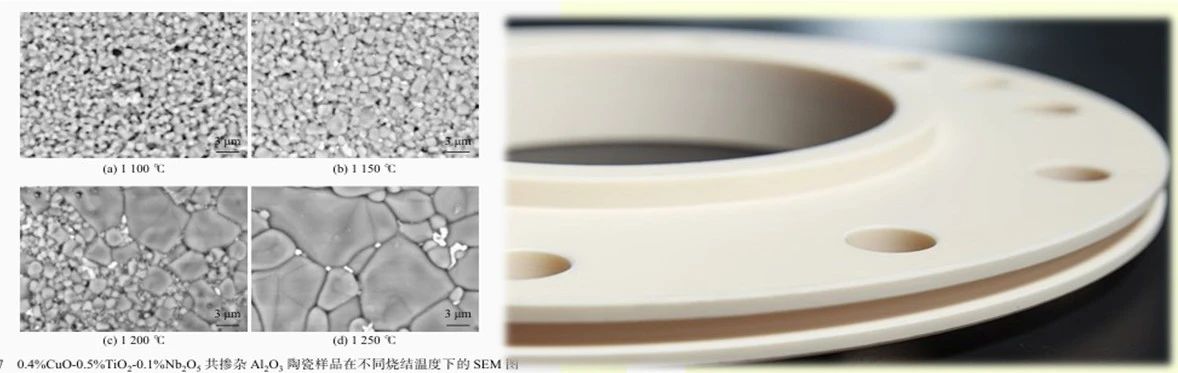
However, sintering generally cannot be carried out automatically because its inherent energy cannot overcome the energy barrier and must be heated to a certain temperature before it can proceed. Sintering is a complex process of physical and chemical changes. After long-term research, the sintering mechanism can be summarized as follows: ① fluidity, ② evaporation and agglomeration; ③ Volume diffusion; ④ Surface diffusion: grain boundary diffusion; Plastic flow, etc. Practice has proven that it is difficult to explain all sintering processes using any single mechanism. Sintering is a complex process that is the result of the interaction of multiple mechanisms. During the sintering process, the main changes occur in the size and shape of grains and pores. Taking the sintering process of
Al2O3 ceramics as an example to illustrate the sintering process of ceramic materials:
Al2O3 ceramics generally contain several tens of percent of pores during growth and failure, and there is only point contact between particles. Under the driving force of reduced surface energy, the substance fills the neck and pore areas between particles through different diffusion pathways, causing the neck to gradually grow and the volume occupied by the pores to gradually decrease. Grain boundaries gradually form between small particles, and the area of the grain boundaries continues to expand, making the body denser. During this considerable process, the connected pores continuously shrink, and the grain boundaries between two particles meet adjacent grain boundaries, forming a grain boundary network: the grain boundaries move and the grains gradually grow. The result is a reduction in porosity and an increase in densification, until the pores are no longer connected to each other, forming isolated pores distributed at the intersection of several grains.
At this point, the density of the green body reaches over 90% of the theoretical density, and the early stage of sintering ends here. Continuing into the later stage of sintering, isolated pores diffuse to the grain boundaries to eliminate them, or in other words, substances on the grain boundaries continue to diffuse and fill the pores, allowing densification to continue while the grains continue to grow uniformly. Generally, pores move along with grain boundaries until densification occurs, resulting in a dense ceramic material. If sintering continues at high temperatures thereafter, it will be a simple process of grain boundary movement and grain growth. The growth of the grain boundary is not the mutual bonding of small particles, but the result of grain boundary movement. The movement of grain boundaries with different shapes varies. Curved grain boundaries always move towards the center of curvature. The smaller the curvature radius, the faster the movement. During the grain growth process in the later stage of sintering, there may be a phenomenon where the migration rate of pores is significantly lower than that of grain boundaries. At this time, pores detach from the grain boundaries and are wrapped inside the grains. Subsequently, due to factors such as the lengthening of the material diffusion path and the decrease in diffusion rate, it became almost impossible to continue with the further reduction and elimination of pores. In this case, further sintering is difficult to improve the degree of densification, but the grain size will continue to grow, and even abnormal growth of a few grains may occur, causing more residual small pores to be trapped deep in the larger grains.
After sintering, the macroscopic changes of
Al2O3 ∝ ceramic body are: volume shrinkage, density increase, and strength increase. Therefore, the degree of sintering can be measured by indicators such as the shrinkage rate, porosity, or the ratio of bulk density to theoretical density of the green body.
The sintering of ceramics can be divided into solid-phase sintering and liquid-phase sintering. High purity substances usually do not exhibit liquid phase at sintering temperature and belong to solid-state sintering. For example, high-purity oxide structured ceramics are mostly sintered into ceramics through solid-state sintering. And some often have liquid phase during sintering, which belongs to liquid-phase sintering. In addition, sintering can be divided into two categories based on the presence or absence of external pressure: pressureless sintering and pressure sintering. Pressure sintering, also commonly known as hot pressing sintering.
Pure oxide or compound powders are formed into green bodies with only point contacts between particles, resulting in low strength. However, through sintering, although there is no external force or chemical reaction during sintering, the particles in point contact can tightly bond into a hard and high-strength ceramic body, driven by the surface energy of the powder particles.
SAT NANO is a best supplier of sintering material in China, we can offer Al2O3 nanopowder, ZrO2 nanopowder, and MgO nanopowder for sintering, if you need other materials for sintering, please feel free to contact us at admin@satnano.com